CJ
Chandan Kumar Jena
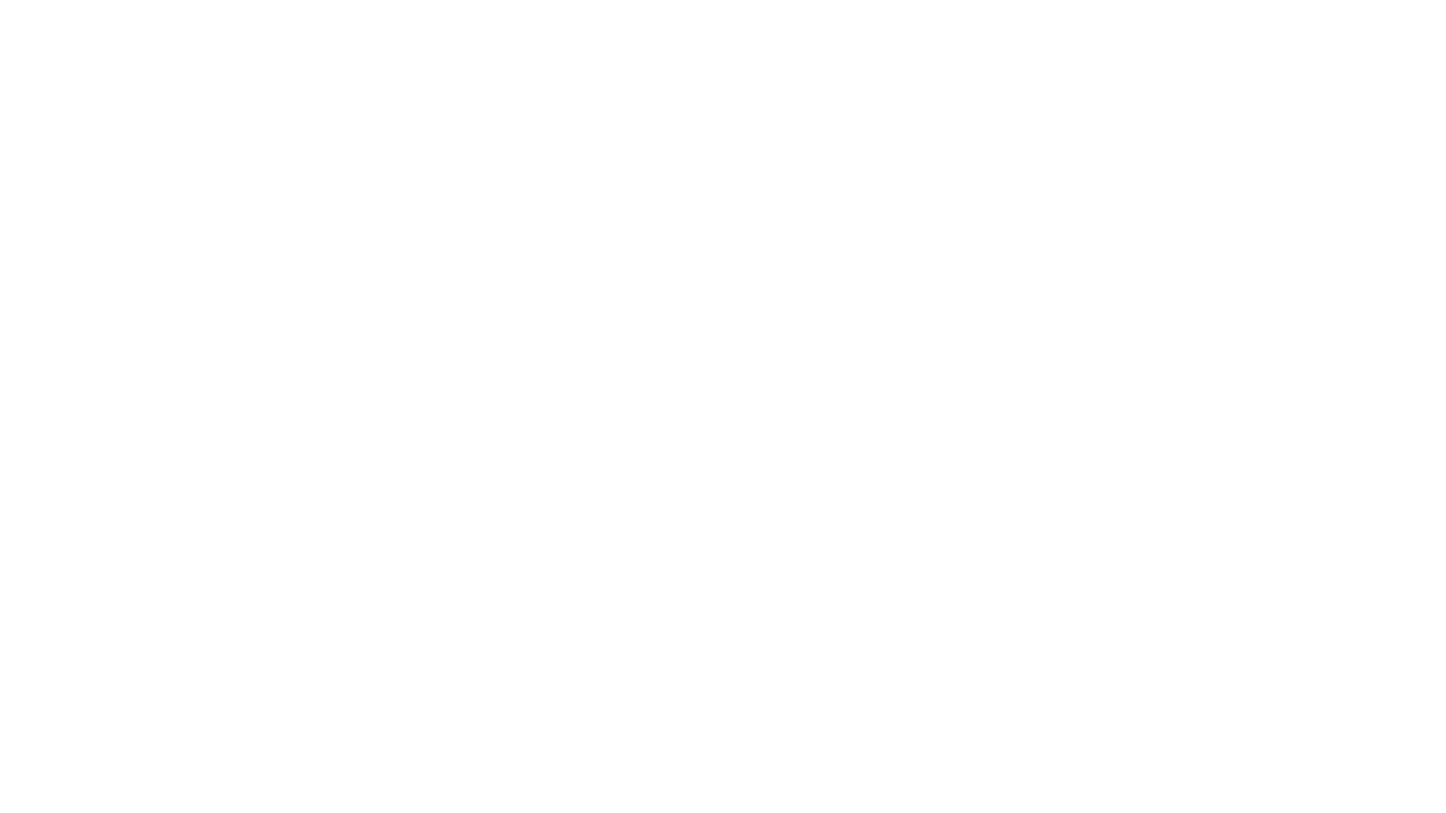
Design & Development of Smart mobility - E-Rickshaw using 3D Experience platform of Dassault Systemes
End to end product designed digitally (used CATIA & DYMOLA) validated digitally (used simulia) & finally launched digitally used (CATIA) using multi-disciplinary apps of 3D Experience Platform.
Inde
PROJECT TIMELINE
We as students of final year of multidisciplinary background (Mechanical, Electrical, Electronics, Civil) from Centurion University made this challenging project a reality with following key objectives:
- Design & development of Electric Rickshaw for 800kg passenger carrier (4+1 seater).
- Low affordable mobility
- Use of digital multi-disciplinary technology using 3D Experience Platform of Dassault Systemes.
- Commercialise with start-ups, Intellectual Property and/or generate employability
- Target Study & Market Identification
- Global e-mobility Market Analysis & Forecast (2017-2025) Survey shows a significant rise in e-mobility sector demand
- In e-mobility expected to show highest growth both in passenger and load body types
- Government mandate to ensure electric vehicles for all by 2030
- Government initiative to install Electric Vehicle Charging Stations at Every 25 kms in India to boost EV industry
- Benchmarking to develop features of Vehicle:
- Studied the different variants of e-rickshaw for different purpose.
- Leveraged VAVE (Vale Analysis Value Engineering) methodology on components /sub-systems.
- Developed ‘Make or Buy’ strategy on sub-systems & components of e-rickshaw for cost benchmarking.
- Product Technical Specification:
- Overall dimension: 2800 *1000*1800 mm
- Ground clearance: 250mm
- Speed: 20-25 KMPH
- Motor: BLDC Motor (48V, 7.5 KW) 900 rpm
- Range: 40-60 km/charge
- Battery Capacity: SLA /SMF lead acid battery (4 nos, 12V, 200Ah)
- Kerb weight: 321 Kg
- Gross vehicle weight: 800 Kg
- Turning radius: 6000 mm
- Seating capacity: 4+1
- System Engineering of Product - Used CATIA-Dymola:
- Benchmarking of all the requirement parameters of e-rickshaw for Chassis, Auxiliary Load, Drive Line, Energy Supply, Control Unit, Environment, Driving Cycle, Driver, others. RFLP approach followed for Requirement Management, through Functional analysis and Logical Architecture Design to end with Physical Design.
- Energetic dimensioning using Dymola for our freeze customer requirement of e-rickshaw like speed, acceleration and range of vehicle, auxiliary loads, road and atmospheric condition, to subsequently determine rating of Motor, gear & Battery.
- Drive line dimensioning, using Dymola to determine all parameters of Motor, Controller, modulator, inverter i.e. resistance and inductance in Motor. Proportional, integral and differential constant of PID controller, Switching Frequency requirements and DC-line capacitor of inverter for ripple free DC output
- Individual system modelling of Motor, battery, controller, modulator, inverter to perform required changes in each model to fit in Functional block architecture
- Product Design – Using various apps of CATIA:
- Designed all sub-system/aggregates and components like steering, power train, brakes, suspension, chassis, Interiors & others based on outcome of System Engineering designed parameters, System, and build CAD model using apps like ‘Part design’ & ‘Assembly Design’ of 3D Experience platform
- Leveraged sketcher app to constrain design dimensions with equations & formulae and make digital model design robust for any changes from iterations
- Used various features of ‘Generative surface design’ to improve aesthetics of e-rickshaw.
- Designed welding using ‘Weld design’
- Performed ‘SHOULD COSTING’ to achieve targeted cost of vehicle with MAKE/BUY decision / strategic with Supply chain base.
- Designed and validated electrical system & Geometry using ‘CATIA 3D part design’ for electrical parts like battery, motor controller and ‘CATIA electrical 3d design’ for routing the wire harness for Headlights – Rear & Front, Indicators & others using bundle segment and multi-branchable.
- Integrated vehicle with vehicle co-ordinate system and intelligent use of ‘Assembly design’
- Simulated vehicle built up/exploded view and assembly/disassembly of e-rickshaw using ‘CATIA composer’
- Product Validation – Using Simulia
- Carried durability analysis for sub-systems – Axle and Mounting bracket and improved design using Structural scenario, Durability validation & Structural model including Pre & Post processing and solving
- Simulated and calculated torsional stiffness, Vertical & Lateral Bending Stiffness for chassis with comparative product for improvement
- Simulated Service Level Analysis (SLA) for various load cases of road using SIMULIA
- Simultaneous Engineering - Using DELMIA & CATIA
- Mechanical & Electrical connections checked for clashes & re-routing
- Manufacturability checked for design parts and improved
- Standardization of parts and part counts improved
- Prototyping- Using DELMIA & CATIA
- Assembled and built prototype digital
- Provided feedback for design improvement
- Digital Marketing/Launch of Product – using CATIA:
- Created visualisation of our Smart mobility e-rickshaw using ‘CATIA live Rendering’.
- Digital Mock-up of Rendered product (Interior and exterior) and presented to college management and examiner during final semester exam.
- We used end-to-end solution of 3D Experience Platform of Dassault Systemes at each stage of product development for our target e-rickshaw with more innovation in digital space. We learnt domain and technology of Dassault Systemes
- We look forward for funding for development of physical prototype and certification of vehicle as start-up.
- It was a great “hands-on learning experience’ and competency development experience using 3D Experience Platform of Dassault Systemes.
Découvrez l'équipe
Auteurs du projet
Découvrez les logiciels
logiciels utilisés
Check my new project