PK
Pradeep Kumar
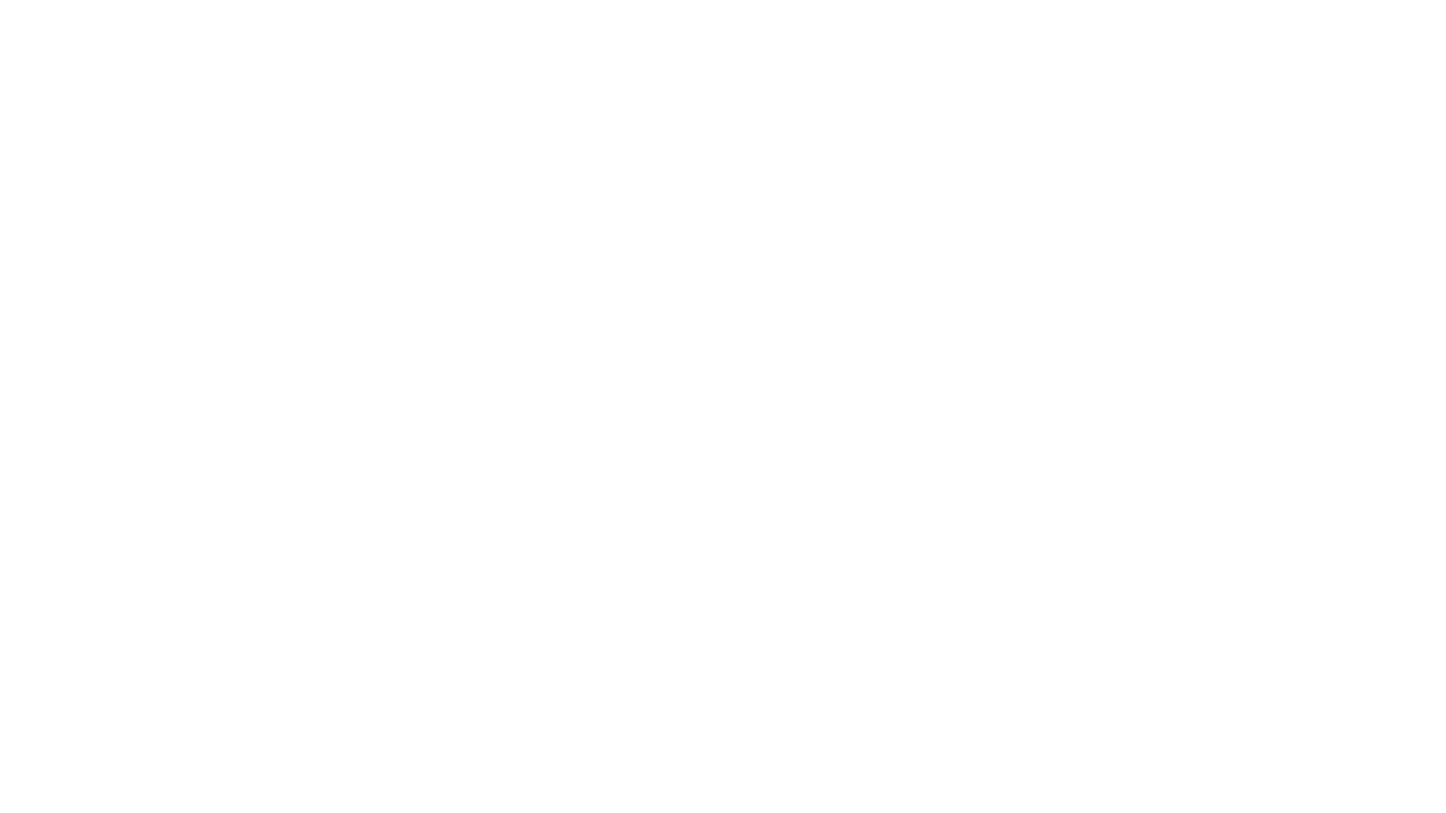
Digital Manufacturing of an Electric Vehicle for capacity of 12 vehicles per day, using DELMIA solutions on 3D Experience Platform of Dassault Systemes.
Make or Buy decision, Process & Facility Planning, Operation creation, Process Graph, Time Analysis, Line Balancing, Key Processes & Ergonomics Simulation on various apps of DELMIA solution using 3D Experience Platform for Small commercial EV.
Inde
PROJECT TIMELINE
Following key approach/methodology is followed using 3D Experience Platform of Dassault Systemes:-
- Business Strategy Planning for Production:
- Lined designed for Annual capacity: 3600 vehicles.
- Volume per day: 12 vehicles (one shift basis).
- Finalised Product Platform/Model: 2 platforms each having two variants.
- Available time per shift: 408 Minutes.
- Takt Time: 34 minutes.
- No of station in Main assembly line: 5 stations.
- Strategy finalised for sourcing of System/Sub-System level: Make or BUY.
- In-house/Make Sourcing: Body shop, Frame Assembly and Final Vehicle Assembly.
- Major Sub-System Buy/Sourcing from outside: All other aggregates and parts /sub-assemblies
- Land: Share & size: 100m x 90m.
- Process Planning: Used DELMIA manufactured item definition, DELMIA process planning, DELMIA time-motion study
- Created Manufacturing Bill of Material (BOM) from Design BOM (EV is design on CATIA). This is based on my Make or BUY decision outlined above.
- Created stations & Sub-stations.
- Created processes as Operation Unit for various fitment, elemental activities for processes, Process Graph (Precedence or successor of process or constraint of any processes).
- Performed Time analysis with both methods - estimated time and MOST (Maynard Operation Sequence Technique) for cycle/Process Time.
- Prepared GANT Chart and carried balancing of line.
- Estimated no of operators/manpower required with full skill level (20 manpower needed).
- Facility Planning: Used DELMIA plant layout design, DELMIA equipment allocation
- Created various facilities needed for carrying processes.
- Assigned product and resources to each operation/processes.
- Digital Factory: Digital Factory is created by design/modelling of following resources using DELMIA plant layout design, CATIA part design, CATIA assembly design, CATIA –AEC/BIM
- Layout Planning with Logistics & Super Market.
- Designed Line station equipment – Pallet, Trolley, Bins, Nut runners,
- Lifting Tackles & Fixtures for Parts/sub-assembly/aggregates
- Civil: Floor, Building/shed/Plant Structure, Portals, Columns, Gangway, Display areas
- Building / Office: Building is designed digitally with CATIA-AEC
- Shop: Fabrication unit, Body Shop, Final Assembly line, Testing/PDI.
- Others: Super Market storage areas, parking area, control unit, security offices, office section for different units.
- Utilities: Pneumatic Air & Water connection – Piping, Power, Forced Draft Ventilation.
- Process Simulation: Used DELMIA assembly evaluation, DELMIA Equipment Design Essentials
- Process simulation is carried out for 5 process to check fitment of parts and its clashes.
- Vehicle built up simulated on Final Assembly line.
- Human Ergonomics Simulation: Used DELMIA ergonomics evaluation
- Carried ergonomics simulation for fitment of BIW and Axle.
- Carried and improved process for Posture, reachability and visibility analysis.
- We experienced and learnt domain of Manufacturing plant using 3D Experience Platform of Dassault Systemes.
- We look forward for funding for setting up physical plant as start-up.
Découvrez l'équipe
Auteurs du projet
Découvrez les logiciels
logiciels utilisés
Check my new project